Structural Engineer Building Inspections
We specialise in structural engineer building inspections, primarily in Brisbane and South East Queensland, but also throughout Queensland and New South Wales.
Our experienced engineers inspect and diagnose damaged brickwork, concrete masonry, plasterboard and concrete slabs. We’ll work out why it’s cracking and how to fix it.
Our engineers then provide rectification advice and drawings specific to your building.
Construction Phase Inspections
Inspections during construction are used to make sure your building complies with the design drawings and Australian standards.
Most inspections can be done by either your building certifier or your engineer. Some inspections MUST be done by your building certifier such as final inspections.
Cornell Engineers can inspect footing, slabs, timber frame and retaining walls in Brisbane and South East Queensland. At the end of the job, we issue our Form 16 inspection certificate to indicate which elements we have inspected.
For other areas call us for a referral.
Footing Inspections
When we conduct footing inspections this is what we look for:
- The correct amount of distance between footing steelwork and the ground (called ‘cover’).
- Correct reinforcing bar sizes as per the plans
- correct footing depth and width as per the plans
- Adequate bearing capacity of the founding soils.
- That tree roots have been trimmed out of the footing.
- The correct amount of lap between reinforcing bars at corners, T intersections and in long straight runs of footing.
- That starter bars are on-site and ready to be installed if specified.
- That the concretor or builder knows what grade of concrete to order to satisfy the drawings.
Problems encountered at the footing inspection stage are usually to do with an inadequate bearing capacity of the foundation soils.
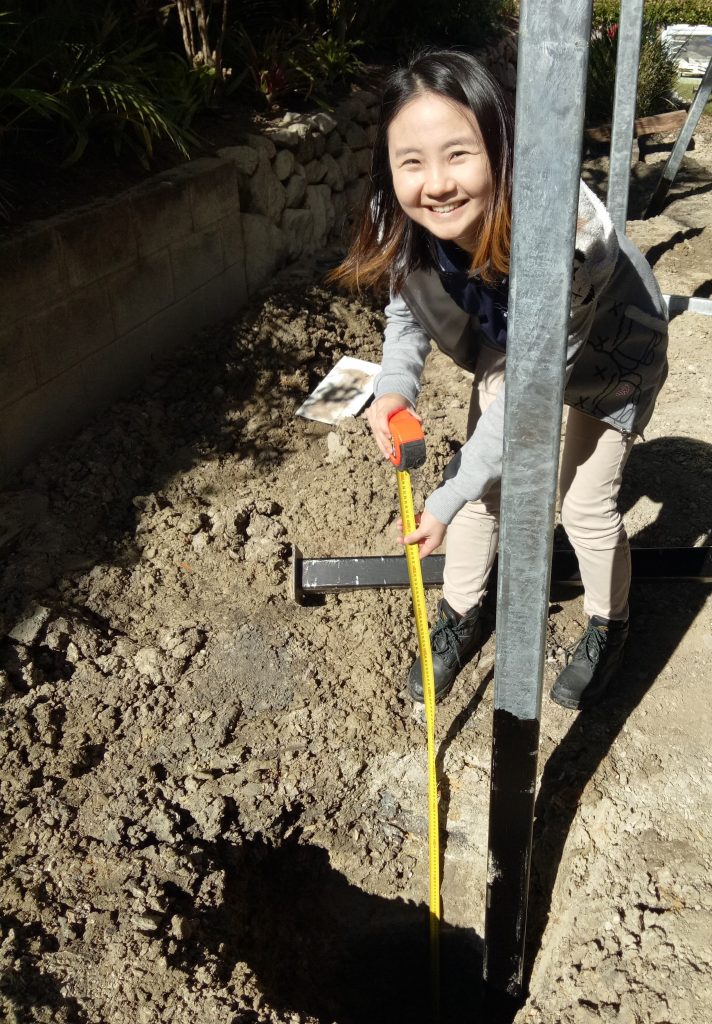
For house footings, I like to test the strength of the soil in the bottom of the footing by pushing an N12 reinforcing bar into the ground. This is my non-technical indicator of the ground conditions.
If it is very easy to push the reinforcing bar into the ground then the ground is probably too soft and either the design needs to be amended or the footing needs to be deeper. Soft ground is caused by high soil moisture content (bad for footings) or loose soils. Both of these situations need to the footing design to be varied by an engineer.
The other main issue at the footing inspection stage is the lack of cover. If the steel reinforcement is too close to the ground when the concrete is placed the steel is liable to corrode and this reduces the strength of the footing.
If you check these two issues for yourself before you call the engineer for an inspection you can save yourself the cost of a failed footing inspection and/or a re-inspection.